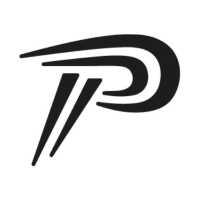
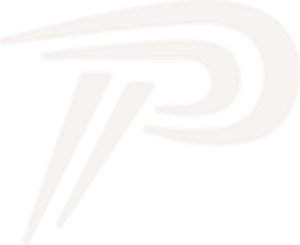
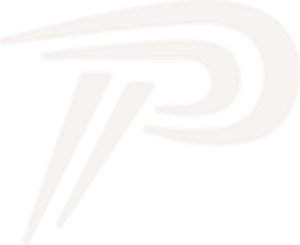
Master Instrument Maker and Repair Person
Bringing instruments back to life and creating dream guitars since 2002.
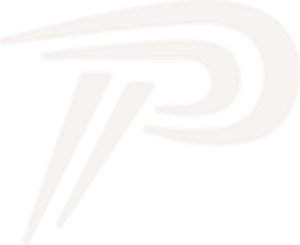
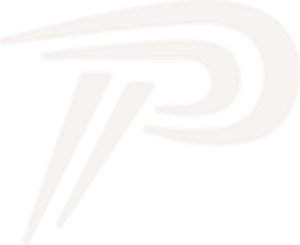
Master Instrument Maker and Repair Person
Bringing instruments back to life and creating dream guitars since 2002.
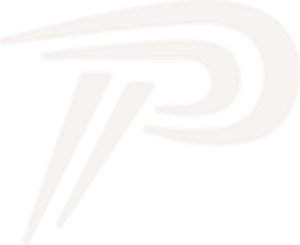
Custom Orders
One off Instruments Created to meet your needs
Bespoke instruments guaranteed make you happy!
Let's get the ball rolling with a message about your desires -
It all starts with a simple message!
It begins with your idea:
Is there a specific shape that you love? A tonescape that you want to create?
What about the custom wound and voiced pickups to get the exact sound you have been wanting?
Unique switching options, top-class finishes... We can help you achieve it.
Our guitars are built to the highest standard, and to your specification. If there's something you have in mind, get in touch, we can deliver it. We work together with you to craft the instrument that you dream of.
Custom Order Process
Place an order with us and be assured that we will create the instrument of your dreams.
We will advise and help guide you through the process of turning your dream instrument into reality.
Creating the perfect instrument for you that you have always desired is our aim.
Over the years I have made many instruments of various shapes and styles, recreating specific sounding instruments or creating something new and truly unique. I am fully versed in vintage and modern construction methods and understand how those options can impact the tone and stability of the instrument. I have a full understanding of how musical instruments function and in my workshop I can make almost every component of an instrument.
The whole process is undertaken in our workshop as we like to ensure the highest level of quality and detail are attained throughout the whole process. You can also be involved in the process if you would like, our sister company guitarbassbuild allows you to come into our workshop and have a hand in creating your own custom instrument, under expert supervision, so that you are truly connected to the instrument we make for you to make for you.
If you have a dream instrument planned out or would like to work with us to create something then we are here to help.
Custom Form
Please fill out the form below to get the ball rolling on your own custom build, if you do not know a detail and would like to discuss options just leave that field blank, this is for those who know exactly what they want so we can make a plan ahead of speaking to youself.
Name *Email *Phone *Message *Body StyleBody TimberPick upsBridgeNeck ProfileNeck TimberNeck JointHeadstock StyleMachine HeadsCreating a Personalized Instrument
We build instruments that are as perfect as they can be, as we intend for you to be the custodian of that instrument. Heirloom quality instruments are the new hype term for high-quality instruments that are designed to last and also in my opinion should not be so complex that they are difficult to repair in the future.
I like to create instruments for you that are highly personalized for you so any details you would like can be included.
There are two main types of instruments we produce, your unique design of the most perfect instrument to meet all of your desires or combinations of instruments, the shape and style you have always wanted to the dimensions you find the most comfortable to use.
We do our best to produce the highest quality instrument that you desire and we demand from ourselves as our craft is our passion in life. We strive to create the most wonderful instruments with an expert eye for the smallest details as everything is important to us in creating the greatest sounding instruments for you. We also understand that an artistic eye is very important to the creation of instruments, as every detail matters as you are going to be seen with your instrument, so creating a unique good looking instrument that meets your requirements and desires is a very important part of the process and I will always work to make sure that this is achieved, as this makes us the happiest of all, I will fight to make sure the small details are correct for you.
We can work using a wide range of styles and techniques from the ultra-modern to most ancient techniques as they all have a place in our workshop. This enables us to use the most appropriate method for a range of tasks and select the most suitable one to achieve the desired results.
Timber Tone Wood and some Construction Details
We can guide you through the process of picking the most suitable materials to create the tonality of your dream build. We will listen to your tonal desires and advise you on the best timber options available for you to get you closest to your desired sound. Using our expert knowledge of how tonewoods interact with the instrument's pickups and parts to create the whole, that is the sound of the instrument we will guide you through the process of picking all the parts required for your build.
Tone Woods and Timbers
I love using tone woods and know that they do make a difference to the tonality of the instrument, my guide of the way you know you have a tonewood rather than a basswood is that the tone of the instrument is different between instruments, the end sound is always a bit different if all the other variables are kept the same. Basswoods are great, basswood is a catchall term for a lot of timbers that are lightweight close grained timbers that are also fast growth timbers. Basswoods serve a function in guitar building in creating lightweight bodies that are more of a representation of the pickups rather than an interaction between the tonewoods and the pickups. Some very interesting things can be done with basswood timbers to create traditional tones or more unusual tones depending on the timber and the materials that are brought together to make the instrument.
I mainly use tonewood with my custom one-off builds as we always strive to create something special and unique sounding. Many of my builds contain figured woods and exotic timbers to give the guitar an extra special unique look. Quality timbers are getting harder to get hold of these days, so I like to keep a stock of the most commonly used timbers so you can choose the exact piece that meets your desired look. I make guitars for the sound they produce as that is the fundamental purpose of a musical instrument. Whilst it is enjoyable for instrument makers to use a lot of highly figured timbers, this is not always the way to go as it can introduce unknown elements to the sound of your build, we are very open about how to create different tonal options with a musical instrument and are always happy to talk about how we should go about making instruments for you.
Desirable timbers
Highly figured and burl timbers. Please be aware that if you want an extraordinary piece of feature timber that these are sometimes hard to get hold of and it can take some time to find the right piece that is suitable for your build, if this is the case when you order we do not take a full deposit until the right piece of material is found. For more details about our exotic timber options please email us for full details of this particular ordering procedure.
Remember that Stradivarius used flamed timbers not because of their tone, it was because at the time these were undesirable materials by the main timber-buying community, at the time these were cabinet makers, the wavy grain patterns found in figured timbers made it harder on your tools requiring more time sharpening as these materials blunted tools faster than plain timber. Some timbers while they look fantastic are in ready supply. Buckeye burl is just popular burl timber, many unique timbers are given exotic names to cover up how common they are to increase their price!
Guitars do not need to contain flashy timbers as the finishing process can elevate a guitar on its own as I do the most wonderful finishing and super paint effects that look fantastic and make for great instruments.
Every part of the instrument will affect the final tone, the most important parts are those that interact with the strings, the pickups are the main creators of the sound. I am a believer that all factors go into making the whole that is the sound of the instrument, everything combined makes up the tone of the instruments I create.
Everything that comes in contact with the string makes a difference such as the nut, fret material and bridge saddle materials as they come into direct contact with the string and thusly shape the sound in the first instance and this carries across to all the other parts of the instruments, there are many nuances when it comes to the timber and glues that can be used that all effect on the tonality. Having studied these options for years we have a great understanding of how an instrument's tone comes together and we use this vast knowledge to plan the very best instrument for you.
Construction Details
Chambering and creating hollow bodies and semi-hollow bodied electric instruments is a personal passion of mine, this style of construction has always offered something unique in the world of electrical musical instruments.
It is a style of construction that has always been part of the electric guitar's history as the first electric instruments were instruments adapted from acoustic instruments, and this style of instrument is still going strong to this day! Their construction offers something special in the world of tone: a more resonant earthy sound compared to their solid body counterparts. Similar soundscapes can be created in solid bodies by using soft timbers with a hard outer shell to make resonating-sounding instruments. Making hollow-bodied instruments and trying to understand the complexities of their sound production is something I dearly enjoy and am always happy to make something along these lines for you.
I always provide updates and advise my customers throughout the build process on the options available as I am creating their instruments and am willing to make changes to ensure their instrument is the perfection they are searching for and making changes along the way finalizing the small details is an important factor of this process.
Electromagnetic Pickups - The Engine of the Sound of an Electric Instrument
The instrument's electromagnetic pickups are the engine of the sound, whilst all factors go into making the whole of the instrument sound the biggest contributor to the overall sound is the pickups.
Now there is a great deal of debate on the internet and some misinformed people believe the pickups are the out-and-out factor in the tone of an electric instrument. Whilst this can be true it is not always the case. It is very easy to cook an experiment and present it online as a fact that proves that the pickups make the tone of the instrument and it is also very easy to disprove this way of thinking. Just nip to your local instrument store and play a range of Stratocasters or watch some videos where people swap their pickguards loaded with the same pickups into different tonewood bodies.
Here are the facts as I see them in as simple an explanation as possible. Overly powerful pickups will overpower the tonewoods and force their sound on the outputted signal of the instrument. A prime example of this was the EMG phase, very powerful pickups that overpowered everything that any guitar offers. I have fitted EMG into many instruments a common one at the time was the Yamaha EG112 guitars and even once into an early 1970s SG and they all sounded comparable with only slight differences as the pickups overpowered the tonewoods in both cases. Les Paul himself did not like the sound of the Les Paul guitar and preferred his Les Paul Recording guitar with the very low output pickups that allowed the timber to speak better. The massive amounts of winds that go into making high-output pickup can overwhelm the timbers used in the construction of the instrument. This can also be combined with extremely powerful magnets that will overpower the instrument's timbers even more.
There are so many factors that go into the construction of a pickup, it is a very complicated thing to wrap your head around as there are so many variables, from the type of wire you can use, from old styles of wire, heavy form build to enameled wire, to the more modern poly coated wires the magnets variations and the physical makeup of the bobbins that are used to shape the coiled wire. Even the elements surrounding the pickups make a difference, metal base plates etc.
Wires
Poly-coated wires are the most common wire used today in manufacturing pickups although the other older copper wire variants are still available, it all comes down to cost at the end of the day. Polycoated wires are typically used for machine motor manufacture and this makes them very affordable whist the old style of wire sees very little to low use in modern motors etc so hence the higher price point. Different wires have different builds to go from one extreme to another the heavy forma wire takes up a lot more space on the bobbin than the modern poly-coated wire. The thickness of the coating changes the spacing of the coils and all of these details affect the final output tone of the instrument.
Now the second point is the space that the winds exist within, think about this; 90% of strat pickups have the same spacing for the winds and we know by changing the spacings of the winds we change the sound of the pickup. Tall and slim with more winds close magnets gives you clarity of sound, whereas a small amount of contact with the magnets and wider bobbin spacing gives you a more bass-driven sound, Jazz Master.
An interesting fact about pickup wire is the gauges the number of the gauge indicates the thickness of the wire 42 is the most common in instrument pickups and the number relates to how many extrusions 1 inch of copper block goes through to reach the correct thickness. 43 is commonly used on telecaster neck pickups and in Rickenbacker instruments, this thinner wire takes fewer turns to reach the same coil resistance.
Magnets
Magnet type and strength are also a huge factor in the tonality of a pickup, this is the way you transfer the physical energy of string movement into the electromagnetic force created by the pickup. It can either be directly or transferred through another magnetic material.
Magnets: there is a range of magnets from Alnico to Ceramic and RareEarth magnets and each of these has sub-divisons that have different purposes that can all shape the final output of the instrument. Most commonly talked about is the Alnico range and for the sake of simplicity we will focus on this main group. Alnico was developed with each type of Alnico having a purpose,
There are many types and variations of Alnico within the Alnico 1 through 9 range, we commonly use in guitar pickups Alnico 2 and 5, although others are used and variations appear in instrument pickups. Alnico 2 is the warmer more vintage sound and Alnico 5 is the modern more shrill-sounding magnet with more power and biting force that musicians tend to like as this more powerful magnet delivers a much greater punch.
Alnico magnets have sub-divisions that all offer differing tones. A great example is threaded magnets which are made from a stronger material to achieve the thread. These are obvious and are some of the most easily identifiable variations you will find although there are many variations of magnet makeups.
Now the magnet fields can either be a direct or indirect magnetic field containing the strings. In the case of a strat pickups magnetic poles are built into the pickup themselves so that is direct, in contrast, the P90 and Humbucker pickups use conductor pole pieces that then connect to the magnets on the bottom of the bobbin to give you a more broader warmer sounding instrument.
There are high-output and low-output pickups and everything in between and we can guide you through the vast amount of choices available on the market today so that we choose the most suitable option for your instrument.
Hardware and Electronics
Hardware is a very important part of the instrument, good quality hardware makes a huge impact on the instrument's sound and the durability of the instrument.
The number one reason for good hardware is tuning, the most important factor about a guitar or bass and something that annoys every musician is the instrument staying in tune, a lot of what you deal with as an instrument repair is tuning issues with instruments and sometimes this comes down to the quality of the materials that make the hardware. Low-cost materials wear out, so whilst they are fine when you buy the instrument over time they become worn out from use and no longer are fit for purpose and have to be renewed or replaced.
There is a large range of manufacturers of hardware that all have varied tolerances to their parts and I will always be on hand to talk to you about the options available so that you can make an informed choice on the parts that go on to your instrument.
Electronics
Good quality electronic parts are very important, these are the parts that interact with the pickup and must be of a high standard to get the most out of the pickups, they can either be very simple or hugely complex, just allow you to do what you need or do a vast array of things that you may find useful. It is very tempting to go all out with the electronic circuit adding coil taps, phase reverses, pickup direct outputs etcetera, although the more the circuit has to it the more potential issues you could encounter in the future, simple is always best in my opinion although the range of sounds you can get from one instrument is quite astounding.
I always use the base level of electronics that is the most commonly accepted within the instrument building community; CTS, Switchcraft and Oakrigsby. I am happy to advise on upgrading them to more modern parts that have advantages over these older style, perfectly functional parts.
Philip Porter Guitars © 2024